Ornua Foods approached Innovus Engineering for assistance in finding a solution to seaming their 189mm diameter, 2.5kg milk powder cans. This represented a challenge for Ornua as most seamers have a limit of up to 153mm diameter. A delegation of Ornua representatives visited our head office in West Sussex to work through a design brief and project scope. They already had an existing canning line, suitable for seaming 127mm and 153mm diameter dairy cans, so we had to find a solution for integrating the seamer into the line with minimal disruption.
In order to avoid breaking the existing canning line, it was decided that a seamer with parallel infeed and outfeed conveyors would be most suitable, allowing the seamer to be positioned against a conveyor section within the line. Once the orientation of the seamer had been decided, we could proceed with the design with a clear understanding of the can handling requirements.
The cans would also need to be vacuumed and Nitrogen gassed, to obtain a residual oxygen level of less than 2%, at a rate of 8 cans per minute.
We would also need to accommodate an increase in throughput at a later date with the option to add a second seaming head, which had to be planned into the design.
Because of the size of the can, the seaming head frame fabrication had to be widened by 40mm. This was to accommodate the wider vacuum seal plates that hold the silicone seal that inflates around the can to create the air tight chamber.
The next stage of the design was to increase the width of the end feed, which again had only been rated for up to 153mm diameter ends. A scaled up version was designed and prototyped, which performed to the same level as the existing assembly under testing.
With a completed design, the 3D model and drawings of our newly named 10VGT were presented to Ornua for sign off. They were impressed with the attention to detail, particularly around the EHEDG design principles, and the simplistic nature of the seamer, which had flexibility built in to run the machine on other sizes with easy to remove change parts.
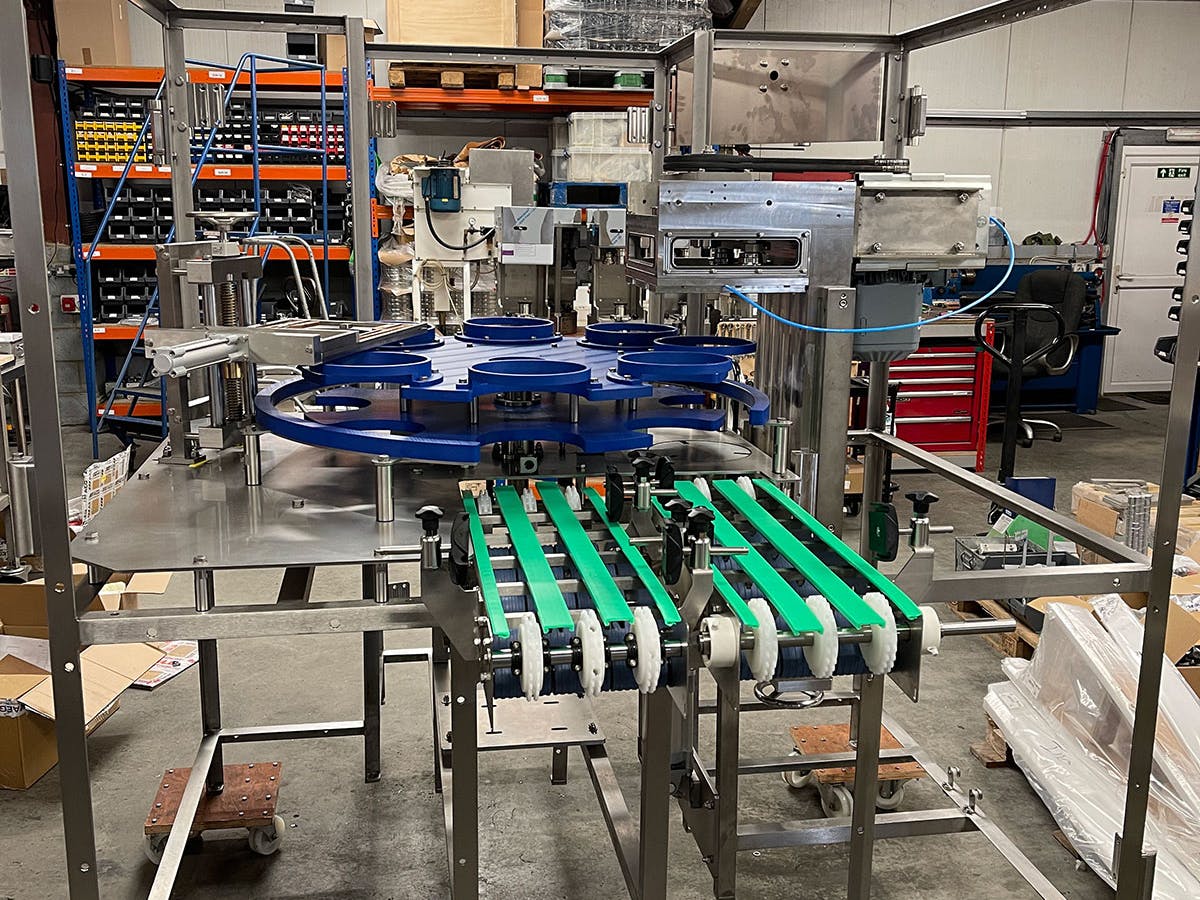
We expedited the parts into manufacture, with a lead time of just 12 weeks from the point of design sign off. All of the components were meticulously machined to ensure surface roughness was minimal and to EHEDG specifications. The frame fabrication was pickled and electropolished for optimal surface smoothness rating.
Once all of the component machining and fabrication was complete, our assembly time was just a couple of weeks before we put power to the machine.
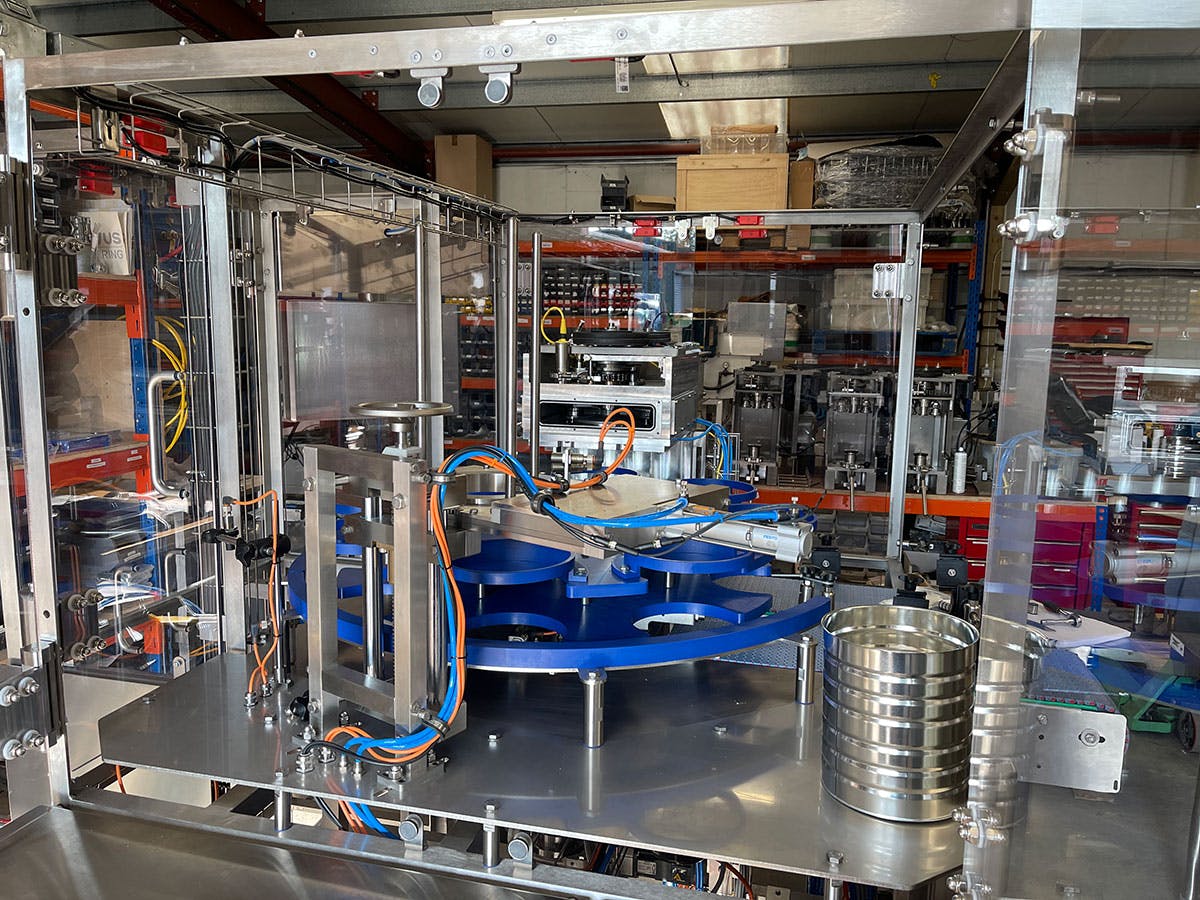
The workshop testing phase was where most of the manufacturing time was spent. We ensure all of our machines are rigorously tested, but put the 10VGT through extra paces to ensure it would pass Ornua's comprehensive factory acceptance test (FAT) with flying colours.
We were able to meet the 8 cans per minute capacity requirement, while also exceeding the residual oxygen target, achieving under 1%.
The seams were comfortably within target tolerances, aided by the vacuum hardened cam that the seaming level cam followers run on, and the adjustable mechanical spring in the lifter, set to 190kg / 420lb force in this instance.
The 10VGT passed the FAT as expected, which meant we could clean and crate the machine for transport.
Using specialist lifting equipment and heavy duty dollies, we were able to roll the machine easily into position within the factory. A two day installation followed, firstly connecting services to the machine, and then running a supervised production to successfully complete the site acceptance test (SAT).
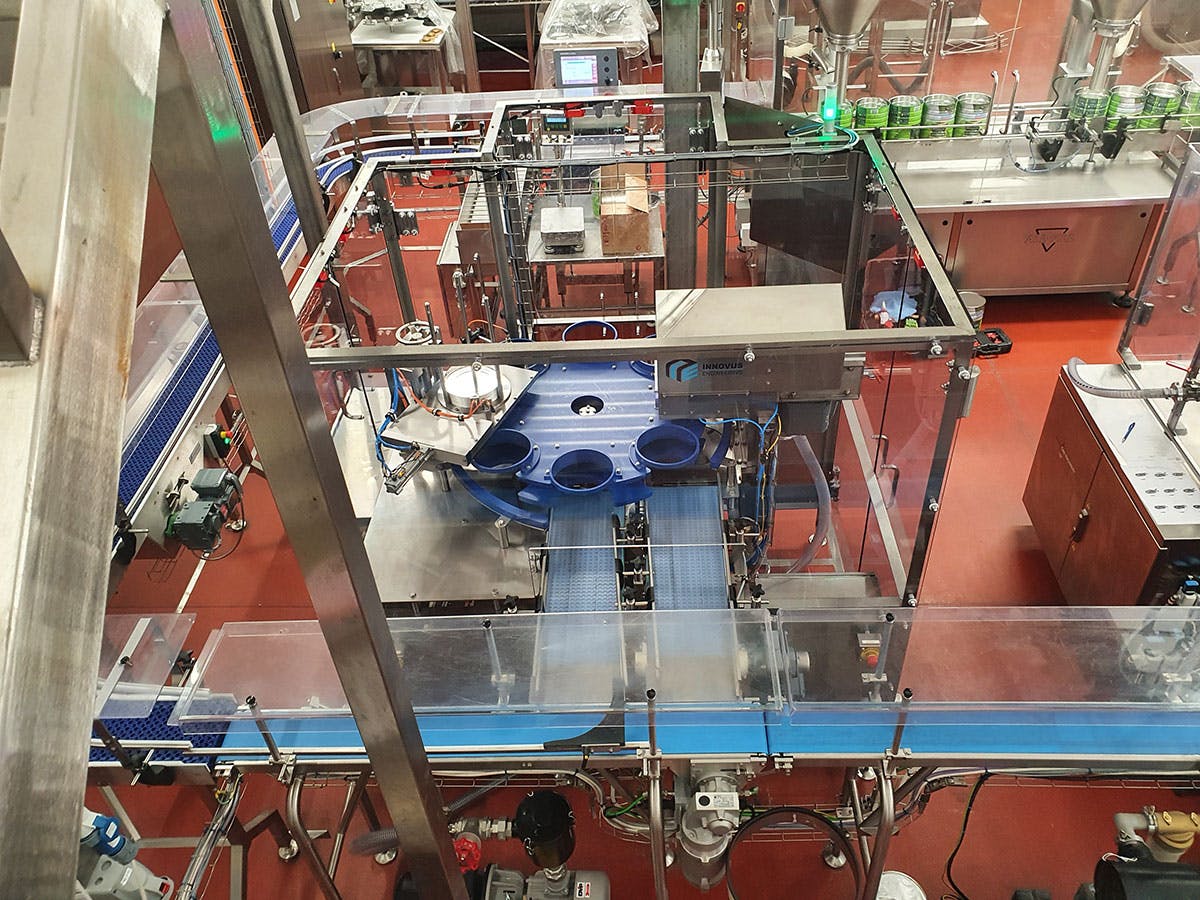
The operators and onsite engineers were impressed with the performance of the 10VGT. Firstly, it was much quieter and more efficient than their existing can seamer which relied heavily on pneumatics. Secondly, there was much less down time, with the 10VGT able to run consistently through a reliable combination of mechanical functions and servo driven automation.
The 10VGT is now a core machine that we offer, primarily to milk powder producers but is suitable for other applications. The option for the second seaming station to form a 20VGT is also a highly requested feature, giving customers the option for less upfront investment in machinery cost.
Contact us today to find out more about how we can assist your milk powder canning requirements, not just in seaming but filling, conveyors, depalletisers, detection systems and full factory controls.